Managing medicine shortages
Every day millions of patients rely on medicines supplied by the pharmaceutical industry.
Complexity of medicine production and supply
The UK relies on thousands of licensed medicines and more than half a million different medical technology products.
Producing these medicines involves strict safety and quality standards within complex global supply chains. Unfortunately, occasionally the supply of medicines fails to meet the demand.
Supply shortages can happen for a variety of reasons, including manufacturing issues, disrupted access to raw materials, bottlenecks in distribution or transport networks, regulatory intervention or a ‘batch failure’ which is where products fail to meet the high quality control standards expected in medicine manufacture.
Companies maintain reserves of products to protect patients from shortages. The size of these reserves is based on a company’s assessments of future demand, alongside any foreseeable disruptions that might impact the wider supply chain. This planning is easier for medicines which come from a single company, for example, an on-patent branded medicine, as they have full visibility of the market. It can be much more complicated to predict necessary reserves for medicines with multiple suppliers, as is the case with generic medicines. Knock-on impacts from one supplier can impact the ability of other companies to cover any shortfall. Occasionally, a sudden change in prescribing patterns can cause unexpected spikes in demand, leading to a shortfall in supply. Another factor might be a complication further up the production supply chain, which impacts multiple suppliers all at once.
Finally, when a new medicine is launched, it can take time to scale up production to meet global demand. Occasionally expanding production can meet with unexpected challenges which take time to address.
Protecting patient from supply shocks
To protect patients it is important for the government, manufacturers and suppliers to proactively identify threats to supply, strengthen supply chains resilience and effectively manage disruptions when it occurs.
This requires an approach that covers the whole of the supply chain – from the gathering of raw materials, through to manufacturing, storage and distribution.
Achieving this requires sustained and effective efforts with international partners, government, the NHS and independent contractors.
Understanding medicine shortages
When shortages happen, companies are required to notify the Department of Health and Social Care (DHSC) who will work with a range of stakeholders to swiftly address and resolve these shortages using tried and tested procedures.
The DHSC has published guidance which outlines the responsibilities that manufacturers and suppliers have to inform the department of any medicine discontinuations or anticipated supply shortages, to help manage supply issues and help prevent any potential impacts on patients.
Companies take their responsibilities very seriously and are accountable to UK regulators should supplies of their products become unavailable.
HRT medicines shortages
The government has worked with the industry to improve supply of HRT products.
The ABPI established a dedicated Project Team of our members to focus on supply chain issues that relate to HRT products. By volume, the HRT market is mainly generic, but we are in contact with government and other trade associations on issues relating to supply.
We are also working closely with our members, the NHS England Menopause Programme and the DHSC Medicines Supply Team to support supplier engagement on HRT and wider Women’s Health Strategy.
You can see our last statement on HRT here.
Addressing shortages
Although shortages in individual products are inevitable in complex supply chains, there are established processes set by DHSC and the NHS for reporting and responding to shortages of medicines and medical products.
-
DHSC is responsible for the continuity of supply of medicines and manufacturers have a legal requirement to inform DHSC of any supply problems.
-
DHSC has introduced the DaSH portal for Marketing Authorisation Holders to submit notifications to the DHSC Medicine Supply Team relating to potential medicine shortages, discontinuations or updates on current medicine supply issues.
-
DHSC has established the National Supply Disruption Response (NSDR), which acts as a single point of contact to maintain supply of medical products to the UK.
-
DHSC have also instituted an Express Freight Service contract to provide emergency logistics for any medical or medical product from anywhere in the world.
-
The Serious Shortage Protocols (SSPs) allows for local pharmacists to dispense an alternative to a prescribed medicine if there's a serious shortage.
-
DHSC reviews its list of medicines that cannot be exported from the UK or hoarded by wholesalers because they are needed for UK patients.
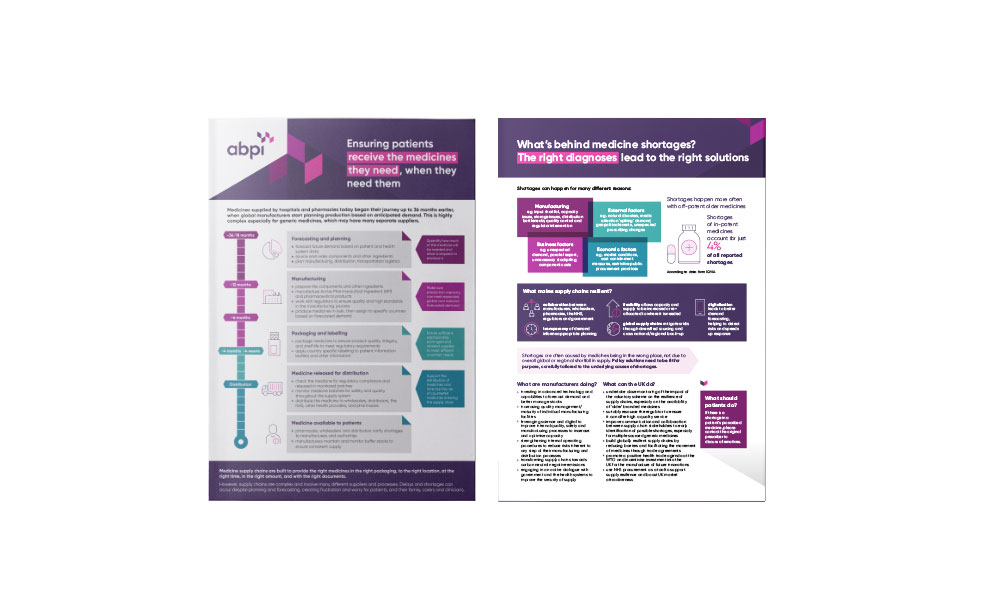
Managing medicine shortages infographic
We have produced a simple resource that shows the journey a medicine takes to reach patients and how medicine shortages can occur.
Related content in this section:
Last modified: 12 November 2024
Last reviewed: 12 November 2024